Editor's note: Dr Magnus Bosse - one of the co-founders - worked closely with MT on the Ultralight project and was responsible for finding many and collaborating with many of the partners who made this project possible. Given the long, sometimes frustrating road taken in solving this challenge, we asked Dr B to share his perspective on making the LW.01 a reality. It complements our video and MT's earlier Design Brief post.
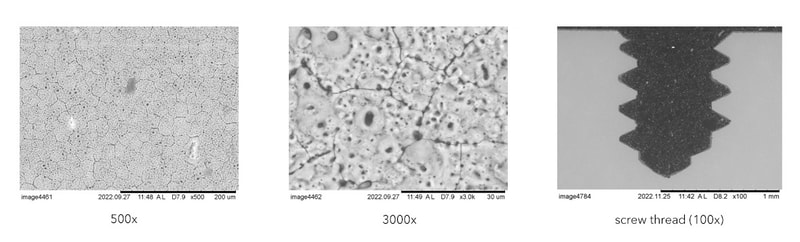
You may recall our recent journal post entitled ‘Design Brief 7: Finding Lightness’ in which MT offered an intermediary but detailed account on the challenges which come with keeping it light. If you haven’t read that yet, I’d recommend doing so before continuing here, as I’d like to focus on the technical implications of producing a very light watch.
As with any design objective to be realised on a physical object, one must first envision it, then identify suitable materials and techniques to realise, and finally test, evaluate and fine tune the whole.
As MT both has ample creativity combined with a solid physics background, any of his ideas and proposals are consistently conceived and usually come bundled with well-founded suggestions in respect to material and techniques – MT’s article gives a good primer on this. But alas, the devil is in the practical details, and there starts a process which I got to enjoy…
It was decided that the new MING LW.01 should be an ultra-light watch with a metal case that still should be wearable, and which should be reasonably affordable. And all of this achieved as quickly as possible. Right from the onset, it was obvious that an exotic, dedicated featherweight movement was out of question (and thus the ETA 2000 was chosen). In terms of materials, a number of advanced Magnesium alloys used in Formula 1, airplanes or aerospace offer the necessary strength-to-weight ratio – something MT already anticipated holistically in the case construction.
But those alloys come with one major drawback for the LW.01 project: their propensity for oxidative corrosion particularly in aqueous environments. Worse even, Magnesium’s high electronegative potential plus the poor protective properties of the resulting oxidative films ensure that corrosion continues well once started. Think about sweat, salt water or air pollution, all of which a watch might be reasonably expected to be exposed to… clearly, we needed a passivating surface treatment to contain that.
That notion initiated a series of trials with lots of setbacks and frustration, but ultimately (and together with much dedication also from our partners!) we persevered.
You might have noticed that in our earlier LW.01 prototypes the bezel, containing the screw threads to hold the watch together, was made in Aluminium and not in Magnesium, resulting in a small but considerable weight penalty. The reason was that the industry-standard corrosion-proofing method we used at that time, anodisation, literally pulverised fine structures like screw threads and so we had to resort to Aluminium for this crucial part.
A new approach came to our attention when our raw metal supplier brought us in contact with the materials scientists from Keronite in the UK: plasma electrolytic oxidation (PEO), which creates a solid, continuous inert ceramic layer on the surface. We commissioned a specialised technical laboratory to subject samples of various PEO-coated Magnesium alloys to a series of real-world scenarios:
- Mechanical abrasion (usual wear)
- Mechanical stress (scratch resistance)
- Salt fog (resembling sea water)
- Sulfuric atmosphere (mimicking industrial pollution)
I still remember fondly the revelation when we first saw the electron microscopy images above – PEO indeed turned out to be a game changer: not only did it prove to provide corrosion resistance to the point that we could actually recommend wearing the LW.01 (within its technical limits, of course!), it also did not affect the structural integrity of the metal (yeah the threads survived and the bezel is now also machined in Magnesium!) and on top of all that, allowed us to use an even lighter alloy (AZ31) than in our original prototypes, which helped shaved a solid 0.8g off the watch!
Finally, we had to address one remaining area of concern, the screw threads. At their flanks we assumed a considerable mechanical pressure if screws are tightened strongly, posing the danger of cracking the hard ceramic PEO layer. We resorted to replace the four steel screws with those made of PEEK composite (this requires a dedicated & very costly mould) which is both softer and by way of construction comes with a particularly smooth thread surface.
Now that the technical base was settled, there were a few aesthetic issues to be resolved still which also hinged on the concept of an ultra-light watch… but this is the subject of a future post!
– Dr. B.
Published: 24th October 2023