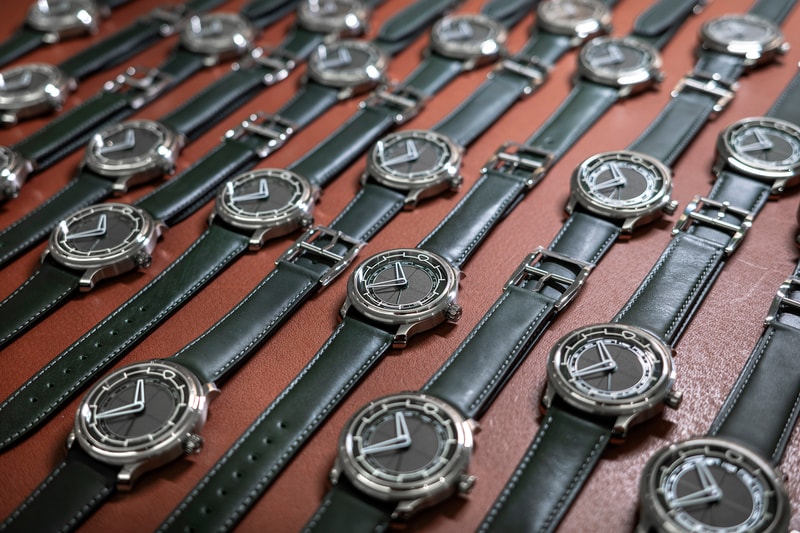
A couple of weeks ago, I managed a ‘first’ – assembling a watch, from the kit of component parts provided to our watchmakers, as would be done with serial production pieces. There are a couple of important things to note here: firstly, whilst I can do some repairs and adjustments, I have never received any formal watchmaking training. (My ‘education’ is littered with a trail of dead movements, munched screw heads and small gears embedded in the carpet – as I’m sure any enthusiast who’s ever tried to wield #0 tweezers will be familiar with.) Secondly, movements are pre-assembled. It makes no sense to do casing around an incomplete movement. Some adjustments to timekeeping rate may of course be made once the watch is cased up and checked on a timegrapher.
On one hand, it doesn’t look like a lot of parts. Everything is contained in a tray perhaps A4 in size, with little divided high-density foam compartments much like a bento box. On the other hand, it still remains daunting for one’s first time as some of the components are not familiar, while others conjure images of black arts like hand setting depth, crystal presses and dial gaskets. I was run through the assembly diagram and our lead watchmaker showed me one example – it took him a good 45 minutes or so, and I know some steps were shortened or not fully completed in the interest of time and avoiding repetitiveness. I was told the benchmark was around two hours on average; plus minus a bit if reassembly was required after exit QC checks. Two hours for one of ours is in comparison to fifteen minutes for a three-hand watch from one of the ‘big three’ houses.
It took me closer to three, and the watch still failed QC.
On the third reassembly, I broke the sapphire dial on removal and the shards landed up scratching the lacquered dial underneath; two components written off. Some things cannot be forced with more time or pressure or repeated attempts; a break is required to calm nerves and steady hands (but no coffee, that’s counterproductive).
It went together okay on the fourth try, and scraped past QC on alignment and cleanliness. The second watch was a bit better; it only took two and a half hours and one reassembly – after discovering that the movement itself was defective, with a canted canon pinion resulting in the hands colliding with the dial at 6, but not at 12.
The model I worked on had several challenges – a base lacquer dial that had to be cleaned very carefully to avoid scratches; a sapphire dial that also had to be cleaned carefully to avoid removing the print, but requiring removal of the primer from printing (normal pad printing ink doesn’t stick to sapphire well), which was also very thin and thus easy to crack; that same dial was set under pressure like a case crystal with a peripheral gasket. The two dials needed to be aligned with the three hands, one of which is independently adjustable, and the top crystal, which carries even more markings, and itself has to be carefully cleaned to avoid damaging the luminous material.
I’m sure by now you’ve guessed the watch was a 22.01 Kyoto; that it takes a skilled watchmaker two hours to clean and assemble a kit for what is one of our entry level pieces is not what I was expecting, and also explains why there are issues keeping up with the production schedule. I’m told the 20.01 S2 and 37.04 take much longer still because there are even more hands and dial layers to align.
The upshot of all this is I realize that we will have to change the way we design and construct to make production and assembly easier, and hopefully also reduce delays and QC issues. I realize that we have hugely underestimated the difficulty in producing these things: just because something is theoretically possible to assemble, does not mean that it is easy to do so in practice. In the meantime, I can say confidently the team is doing the best they can, but some things simply cannot be rushed if we want a good final result. MT
Published: 16th March 2023