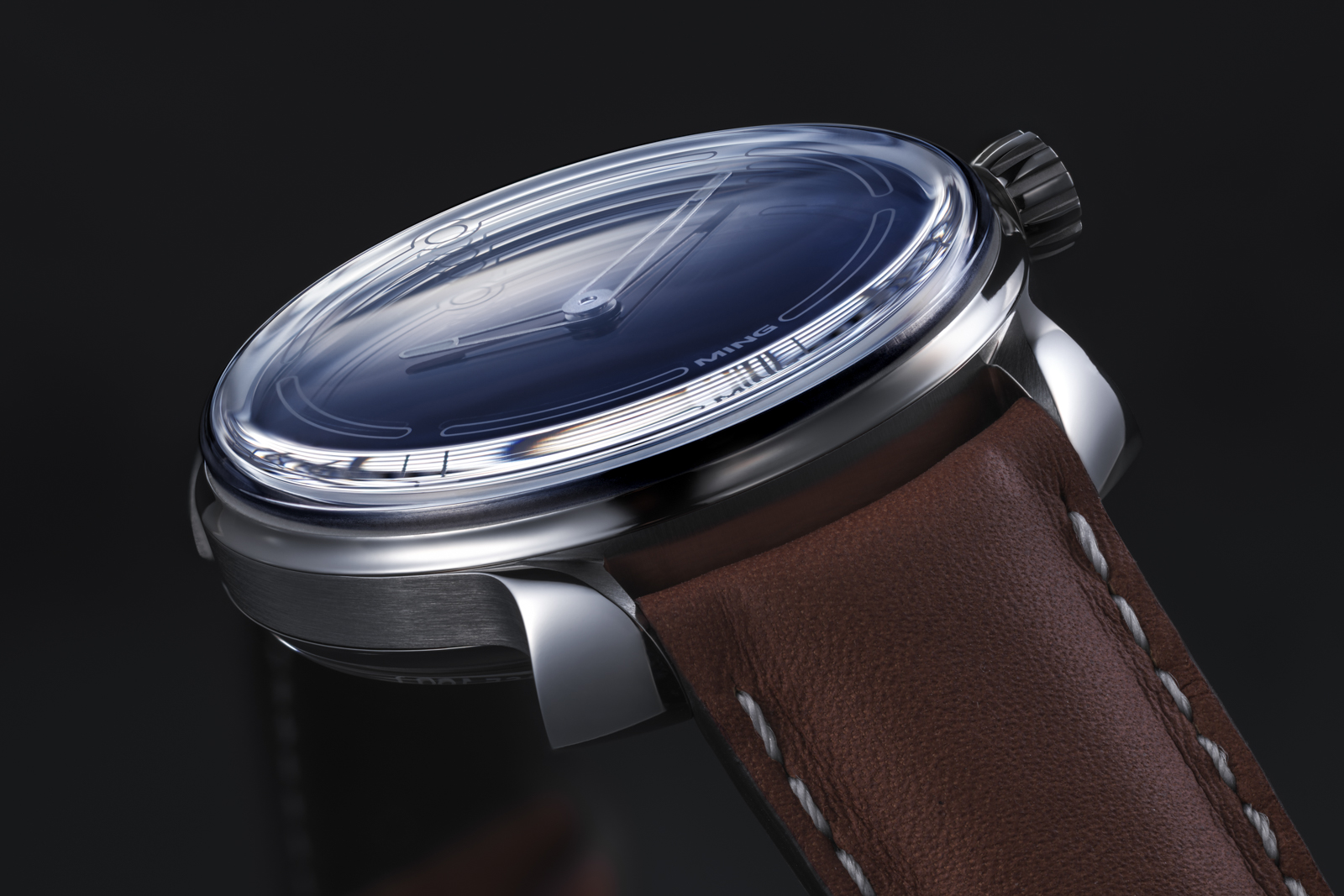
The 19.01 is not a conventional watch, nor a conventional design, and for that - it would only make sense with something other than the usual material choices. Firstly, we skew away from precious metals that are non-functional as this contradicts our philosophy of value; this leaves materials such as steel, titanium or bronze for the case. The latter can cause issues with allergies, and personally, we’re not so fond of the aged aesthetic - it doesn’t suit our design language.
Steel is a much colder feeling material due to its heat transfer properties: higher thermal conductivity than titanium means that it transfers heat faster and doesn’t have the same organic feeling on the wrist, especially when you first put the watch on. Given our desire for a mixture of brushed and polished surfaces on the watch, grade 5 titanium (in reality, a titanium-aluminum-vanadium alloy) was the only choice: pure (grade 2) titanium has a different aesthetic - it’s darker - but it cannot be polished without oxidation spots.
The 19.01’s case really needs these alternating polished-brushed interfaces - the concave polished bezel has texture without visibly identifiable reflections, plus forms a visually continuous interface with the curved box sapphire; the brushed caseband gives a sense of solidity, and the polished convex lug tops emphasise the ‘MING twist’. The crown’s form does the same - it’s a mixed of polished (outer); bead blasted (inside fluting) and circular brushed about the logo (the axial end). Edges are radiused to 0.1mm to prevent sharp edges, but retain crispness.
Traditional haute horology finishes on a movement involve polishing of functional surfaces and brushing of others; polished anglage on plates and bridges, and some form of striping or perlage on the surface of the bridges themselves. The higher the polish, the deeper and more three-dimensional the stripes, the higher the assumed level of finish. Whilst these are visually beautiful and mostly functionally justified, they simply do not fit with our design language. We elected to retain the high grade functional finishes on working surfaces (i.e. black polished pinion leaves, pivots etc) and anglage on bridges, our desired aesthetic is more modern and technical - and the movement should be, too.
The movement baseplate and bridges are two very slightly different tones of anthracite grey to offset each other and give a much greater sense of depth than the physical dimensions would suggest; the dial side is darker to afford better contrast and visibility to the front sapphire etching (since it’s visible through the dial). The rear side is toned to visually continue into the case itself, which employs no spacer rings for maximum rigidity. This is necessary for the 19.01’s construction as a very rigid surface is required to mount the box sapphire crystals without the risk of separation.
The lower movement plate is bead blasted, but the upper bridges are not - bead blasting would soften the edges of the anglage, so the surface is actually very finely rough-brushed before coating. Even the anthracite coating itself is a deliberate choice for longevity: unlike conventional nickel plating, it’s difficult to stain or pick up oil, and completely protects the bridge surfaces from corrosion. Best of all - it fits the personality of the 19.01 perfectly.
- MT