We realize not every detail is obvious at first glance, so this series is intended to provide an inside look into the thought and design process behind our creations – and yes, perhaps a sneak peak or two at the future.
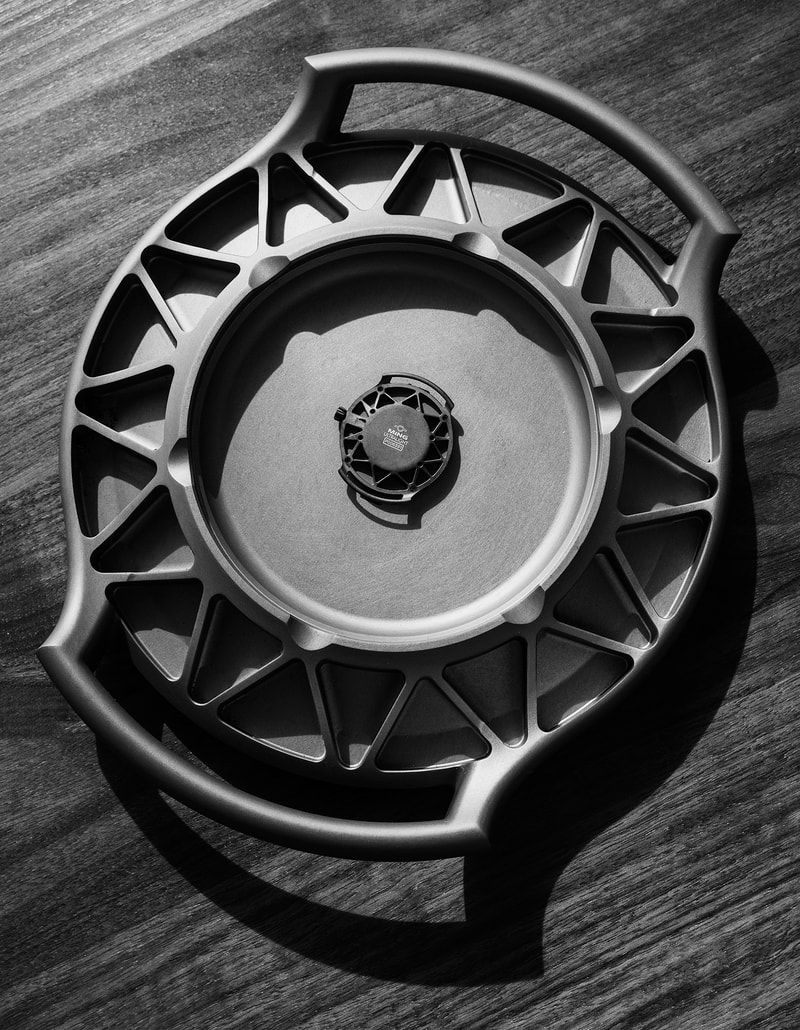
When I took on the challenging of designing what will probably be the world’s lightest mechanical watch* - I honestly thought it would be a case of selecting the right materials and figuring out how far we could push the machining. As it turns out, that’s only partially correct; challenges came in forms we did not expect, and the machining part was actually the least of our concerns.
*In production, wristwatch, mechanical, yada yada – it’s difficult to define exactly what this category entails; do ring watches count? That would be unfair as they save material by not having a strap. Or how about a paper sundial with some tape? You can see where this is going.
That said, it’s some pretty cutting edge stuff: blending the limits of machine precision and repeatability to make 0.5mm wall thicknesses from WE43 magnesium-yttrium-neodymium-zirconium alloy; using finite element analysis to determine exactly where we could remove more material. Even the edges of the support ‘spokes’ are beveled to both prevent nicks and dents, and yes, save a fractional amount of weight. It’s also less dense and more finely machinable than carbon and not as flexible at the same thicknesses (or thinnesses).
We rethought the entire concept of a case to minimize the material used. The dial periphery is also the movement support; the case ‘ring’ is also the caseback; and the markings are printed onto the crystal – which by the way isn’t sapphire, because it’s too heavy. Instead we are using the latest generation of Corning Gorilla Glass, because it has only 60% of the density and after AR coating, the same hardness properties as an AR coated sapphire – since it’s the coating that’s the outermost layer on both materials.
The bezel, unfortunately, is not WE43. This pains me because it cost us a not insignificant 0.25g; enough to put the weight up a main digit. The reason for this is because it contains the threads for the four screws that hold the sandwich together; if these threads were in WE43, they wouldn’t survive the chemical and coating process we use to treat the surface to render it inert and corrosion-resistant. And yes, we tried.
There are other extremes: the buckle is WE43, and has an XL-sized skeletonized MING logo to save more weight; it’s about 0.6g. The strap is a single piece and single layer of alcantara and forgoes traditional loop, stitch and springbar to close the end – because glue would be too unreliable, and springbars (steel) and stitching cost more weight than the having the lugs built into the case (and thus made of WE43). It weighs a hair under 1.2g.
Here is the point I admit we could have saved even more weight by making the watch smaller and using some exotic movement with filaments and strings; instead we used a standard (but admittedly not that common) movement, with automatic winding, put it in a metal case and kept the size a wearable 38mm, with water resistance.
Why? Because I still fundamentally believe a watch should be usable for its intended purpose, i.e. telling the time and reasonably wearable. I’ve been using a prototype for several months now on my bike rides, subject to all the vibration that entails. I also hate that plastic feels like plastic – it has the wrong thermal conductivity, and too many associations with cheapness. Finally, being the masochists we are and having started a watch company after all – it was more challenging to do it this way. Just wait until we reveal the final weight figure. MT
Published: October 2022