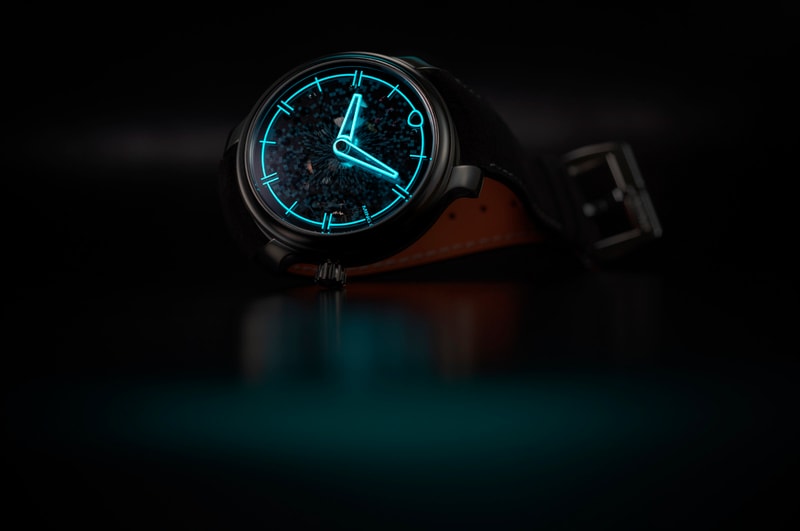
We realize not every detail is obvious at first glance, so this series is intended to provide an inside look into the thought and design process behind our creations – and yes, perhaps a sneak peak or two at the future.
When we moved to the second generation design language, we wanted more distinctive hands that would be part of the instantly recognizable elements that make a MING... a MING. This meant that they would have to be bolder and larger, and I also wanted to address the usual size differential between hour and minute hands: typically, the implied size starts from the same effective point, meaning the hour hand has to be much shorter to be instantly readable and not confused with the minute hand. But in our case, by segregating the pinion surround with the minute hand, it is possible to create a hand set that’s nearly equal in length (so it looks more balanced) but yet well differentiated (for legibility).
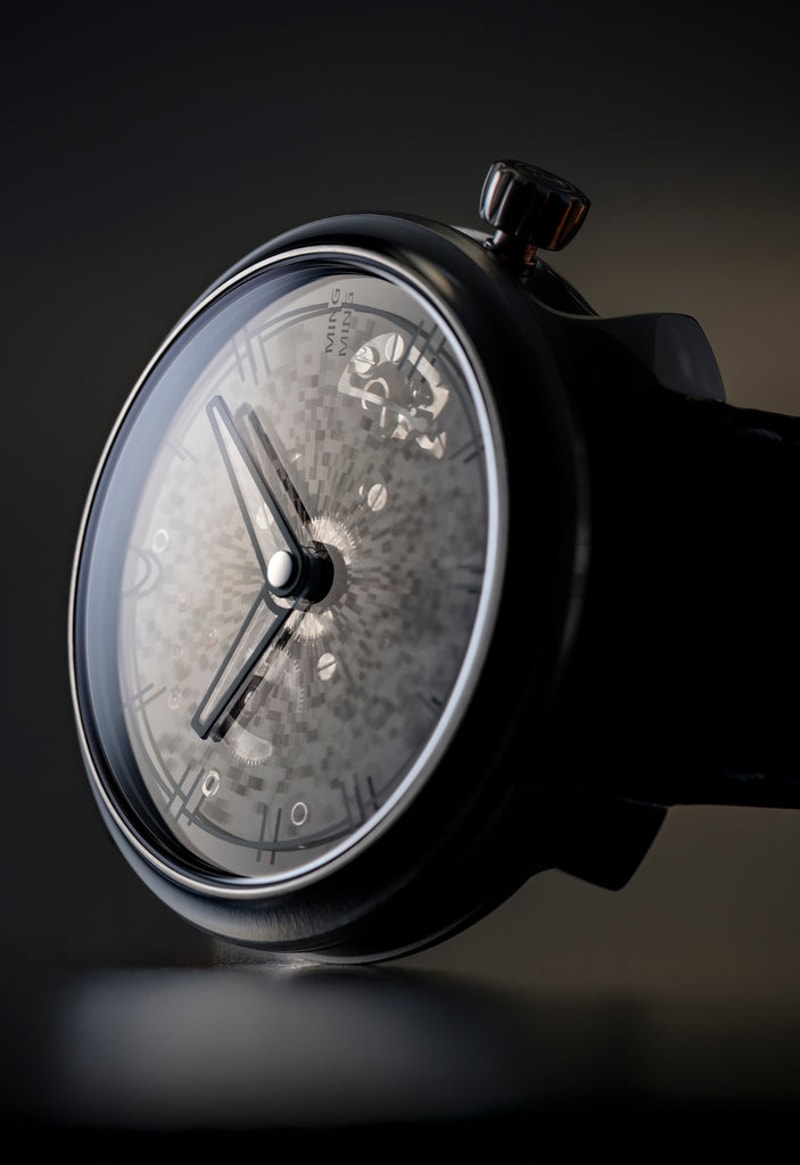
But doing this also of course increases the hand area; if it were solid it would simply overwhelm the dial. Therefore, to maintain harmonious proportions, we went down the skeletonization route. This process limits the amount of luminous material you can apply to a hand; either it’s in a narrow channel between the inner and outer loops (and like most traditional luminous material, applied liquid and held in by surface tension), or a solid block (which is difficult to cut to that thinness and retain clean edges and sufficient rigidity to mount) – or the third solution, which is a thin and flat brass hand that has a layer of luminous material applied on top. This is the approach we took for the 17.09, 22.01 and 20.01 Series 2.
In the meantime, we were developing another process to further improve the brightness of overall luminosity and render the hands with the same level of definition as the dial – naturally, ceramic Super-LumiNova X1 in sapphire. We feel this is the ultimate solution for luminous material at the moment: the edges are defined by a laser cut cavity, meaning very high definition small features are possible (for example, our logo, or tachymeter and pulsometer scales) and brightness can be controlled by overall depth of the engraving. Lastly, due to the nature of the process (fused luminous material without binder) – it can be very bright, very dense, and very long lasting. In a hand, this means a very bright and three-dimensional luminous structure is possible – as well as one that radiates light in all directions and in turn illuminates elements around it.
However, there is a very big challenge transferring this technology to hands: a dial only needs to be polished on the surface after application of HyCeram. Hands are significantly more complex as there are no fewer than six steps. Firstly, channels are cut in a large sapphire blank, to hold the luminous material and define the inner limits. Next, the luminous material is baked at several hundred degrees to fuse it to the sapphire. The top surface is polished to remove excess and leave a smooth surface again. Then, the actual hand shape is cut from the blank – edges and tube hole. The flanks must then be polished, which is a very high failure process due to the thinness of the sapphire (remember, half the hand height is now luminous material, leaving barely ~0.2mm of sapphire). Lastly, because sapphire is not an elastic material, separate metal tubes must be fitted and cemented so the hands can be mounted to their respective pinions.
Complexity, cost and the complex supply chain combined with the limited number of partners capable of doing these operations is the reason we have only used it in two watches to date: the 20.09 Tourbillon, and the 20.11 Mosaic. Both watches share the same pinion fitting (and thus hands; 20.01 Series 2 does not have sapphire hands because there is insufficient clearance between the four concentric pinions); even in production quantities, one set of sapphire hands is comparable in cost to a whole 17.09. Unfortunately if any one of these process fails, the entire batch is a write off and must be discarded. Trying to standardize and improve the production process is an ongoing challenge; but we do so to hope to be able to offer this unique feature on more models in future.
- MT
Published: May 2022