In this second installment of our report on Manufacture Schwarz Etienne, our partner for the 19-series watches, I will highlight some of the more special watchmaking skills that give birth a MING 19.01 or 19.02.
Creation starts at the heart
That watchmaking at our Schwarz Etienne goes particularly deep into the heart of the matter is no secret anymore after Part 1 of this series. In summary, they not only produce bridges, wheels, but also the entire escapement. They even construct and specify a great number of the machines needed. Very few watch manufactures actually possess such manufacturing depth and capabilities, and thus a considerable degree of flexibility and independence!
Since the escapement is made in-house, one particularly involved aspect in the creation of a watch at Schwarz Etienne is the assembly of the pallet. The two forks made from sapphire have to be seated and aligned into the fork with utmost care and the right amount of shellac.

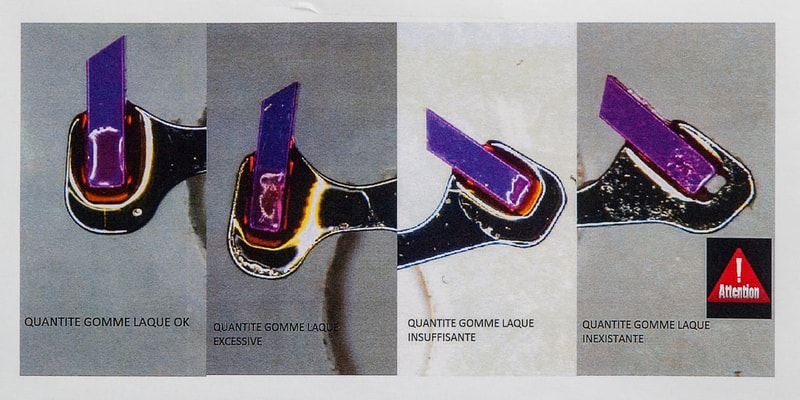
With the components for the movements completed, watch kits are handed over to the assembly atelier. Here, I had an eerily familiar flashback to my time as a molecular biology student: laminar flow benches ensure that only filtered, dust-free air flowed around the emerging watches. This is a godsend and absolute necessity given with the partially skeletonised movement and the sapphire dials we use in the MING 19-series. Any dirt or debris would be painfully obvious and on display.
I won’t spend much time describing how the movements are assembled - this is essentially similar to the process at most manufacturers. Let's just say that the watchmakers at Schwarz Etienne have ample experience with ultra-flat and open-worked movements - skills acquired at the most prestigious watch manufactures in Switzerland and experiences that come quite handy when creating the MING pieces.
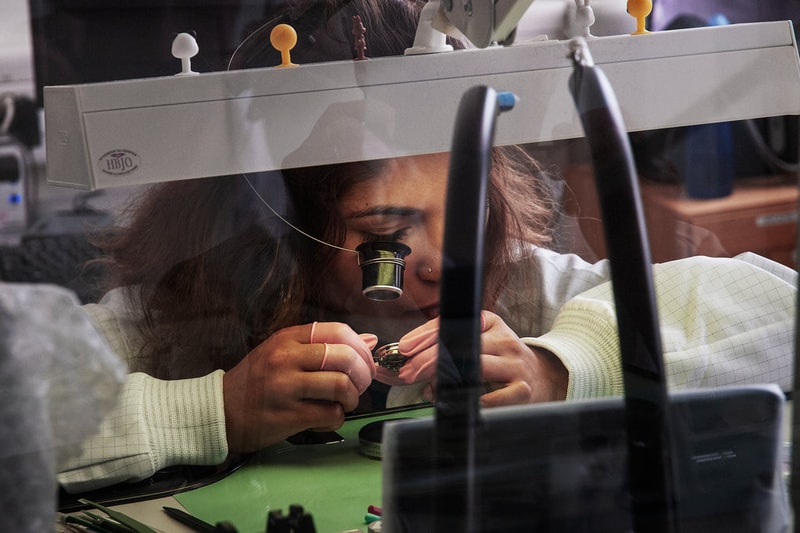
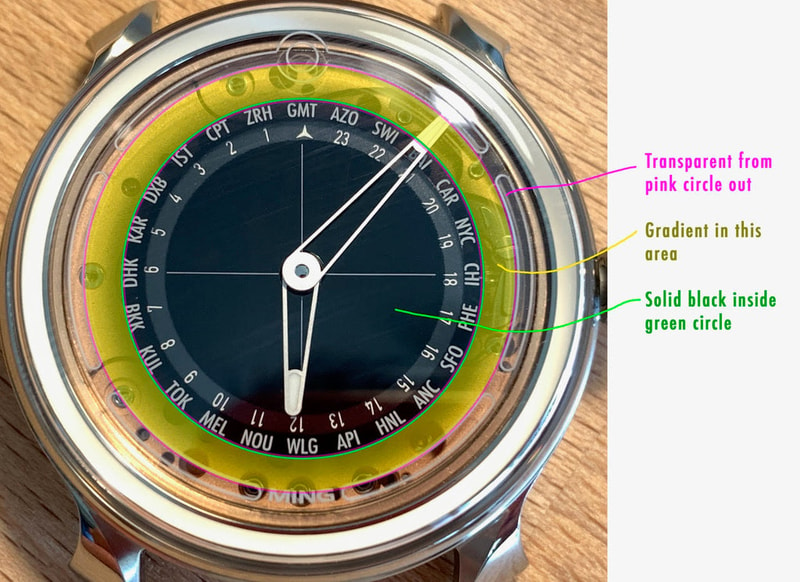
Gradual transparency - a surprising ‘complication’
Our sapphire gradient dials are a good example of unique production challenges. First of all, there is the gradient itself; while there are a number of watches on the market that come with ‘fumé’ dials, these are not transparent and the gradients are applied to metal not sapphire crystal. We were a bit surprised ourselves to learn how complex it is to apply a smooth, consistent and well defined colour gradient on a sapphire dial. In fact, we had five dial specialists experimenting with a number of different techniques, but only one succeeded and in the course, developed a new process that requires precision and careful control. Take the dial of our new 19.02 Worldtimer, where the fade starts at the outer edge of the 24h ring and so gives us a very small working area to achieve this effect.
Yet this is not all: the transparent nature of the dial requires that all surfaces on the dial side of the watch - the movement plate and both sides of the sapphire disk - be perfectly free from dust. On a solid dial the movement plate and dial underside would be hidden from view. Further, since the gradient paint is applied on the underside of the sapphire dial, tremendous care is needed during assembly and adjustment of the watch, especially with the 19.02 and its additional 24h disk sitting right beneath the dial. One scratch and the dial cannot be used anymore.
The final fitting of the dial and hands to a 19-series watch are done only in a state of tranquility and concentration, with the watchmaker working on one piece at a time, slowly and carefully.
Due to the vulnerability of the paint on the dial, the hands are mounted tenderly, with experienced hands making sure that the dial is not touched and does not move or rotate on the movement. In practical terms the watchmaker has to set the hands such that they do not require any further adjustments after they are seated on their axes - everything must be done in one single careful step.
The clearances between the hands and dial are tight, which is another reason why we at MING benefit so much from the solid experience that Schwarz Etienne’s watchmakers possess.
Despite the filtered air in the watchmaking cabinets and the care with which the watchmakers work there is still the possibility that dust particles precipitate. Those are removed with rubber gum or with a stencil made from soft wood before the front bezel with the crystal is mounted to check for free movement of the hands between the front crystal and dial.
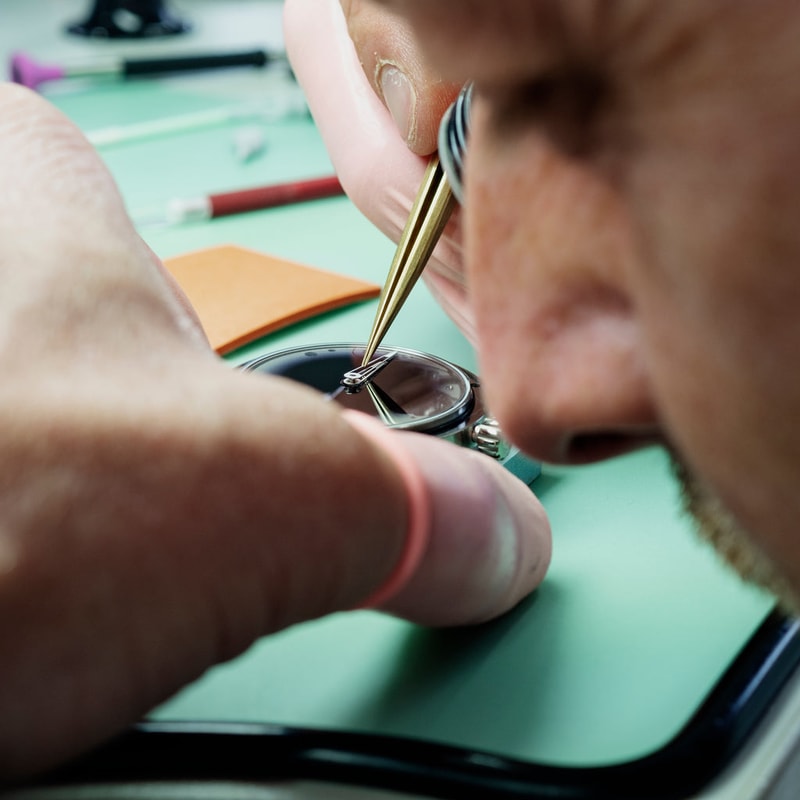
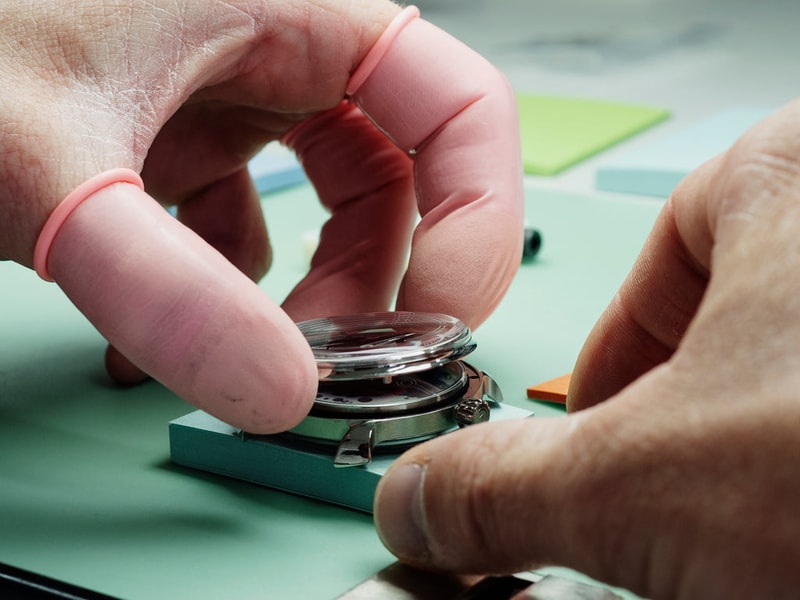
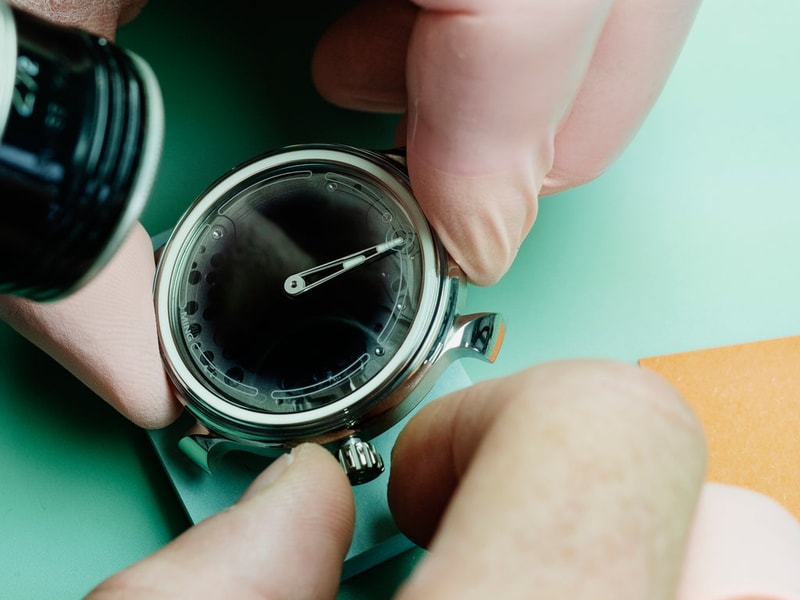
Comprehensive checks
With the depth of manufacturing capabilities at Schwarz Etienne, one is not surprised to learn that they take timekeeping seriously. Even with the MING 19-series that comes without a seconds hand is throughly run in and tested for accuracy in each position, over a period of nearly a month, with detailed recordings of its performance.
Even we at Team MING take our watches seriously and regularly travel to Switzerland to discuss progress, evaluate technical or aesthetic options, and above all to personally inspect and quality control each single batch of MING 19.01 or 19.02 watches. In contrast to the industry standard of a visual inspection with the naked eye in 30cm distance, our benchmark is visual inspection at 15cm with the naked eye.
Editor's note: we've been asked several times why watches are not inspected with a 6x or 10x loupe. Watchmaking, especially at the level that Schwarz Etienne performs at, requires a lot of skill and manual work. Perfection is impossible. We can get very close to it, of course but there is a point of diminishing returns.
We spend a lot of time on a plane and in airports to bring Ming Thein’s ideas into reality, which makes the fact that our young brand has produced two watches with a timezone function, the 17.03 and the 19.02, not so surprising. It is a tiny bit motivated by the egoistic desire for a wrist companion that allows us to better coordinate our efforts.
- Dr. B.
Published: April 2019