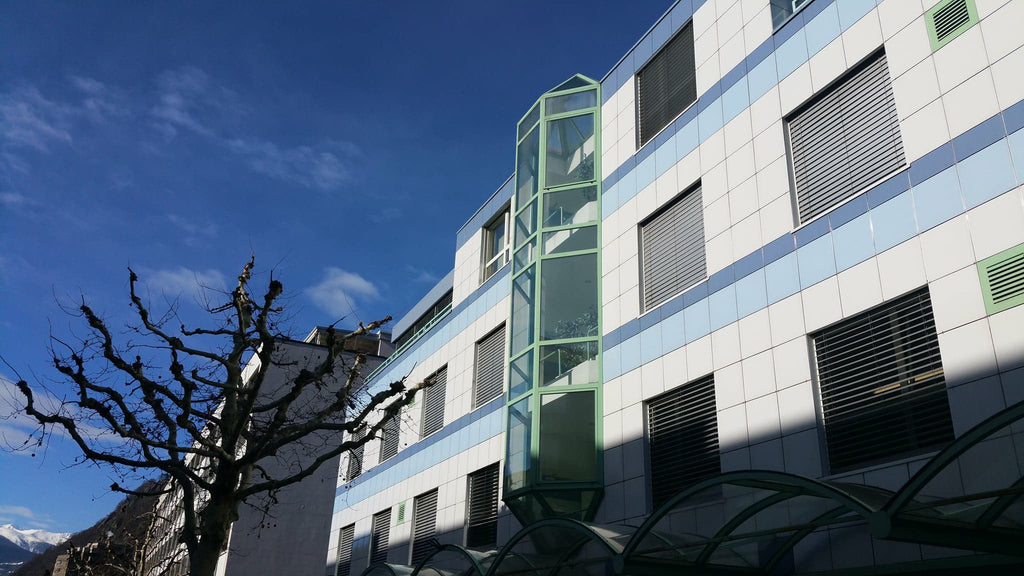
While the 17.03 is, from a purely technical point of view, a simple watch - it features a number of construction details that pose several challenges for our watchmakers. The MING team went down to the south of Switzerland to spend a day in the atelier that creates the MING 17 series.
When we conceived the MING 17 series as our entry level range of watches, we were driven by the desire to offer our customers as much design refinement and watchmaking value as we thought possible. This is how we came up with the multi-part dials, the rugged titanium cases, as well as the 250hr testing programme for each and every MING watch. All these details have profound implications on the production process, as we found out earlier this year when we visited our production partner.
Our production partner for the 17 series works with several large and widely known watch brands. The firm has well-equipped workshops that are capable of producing significant numbers of watches in relatively short time. However, due to its peculiarities, the MING 17.03 is not assembled in the main production line. Instead, the 17.03 (like our debut model, the 17.01), comes to life in the hands of experts at the Specialty and SAV (service après-vente; after-sales service) Atelier. And you'll soon see why: there is much more hand-work and individual adjustment involved than with a watch with a more conventional construction!
Doing a proper job: twice the surfaces to clean…
It starts with quality control for the dial and case components as well as the removal of dust and production residue. Recall that the dials of the 17 series are not only composed of several parts, but also have a signature sapphire donut around the circumference: this detail alone adds two surfaces (if you count the rim - three) which need to be painstakingly cleaned from any contamination as particles or smudges would be immediately visible.
Because the ring is made of sapphire with thickly printed Super-LumiNova C1 (we use a 30-layer coating process on the sapphire donut to build up the material to a thickness of 0.3mm) the usual dose of compressed air is not sufficient to get rid of all the dirt. Each single donut is individually inspected a second time and remaining spots are cleaned with specialty adhesive paper (actually quite similar to the famous Post-It notes).
Once ready, the donut is placed into a clean silicone bag. For completeness, the remainder of the watch encasing, such as dial plates, crystal and case, are cleaned with the same care. Just to give you an example, the lugs of the 17.03 contain two sets of holes to mount straps and bracelets, respectively, which we had marked with a ‘C’ (for the strap holes) and an ‘I’ for the bracelet.
These indications are laser-engraved to the titanium case, a process that produces heat and thus leaves light scorch marks on the back side of the lugs. Due to the shape of the lugs as well as the case finishing the marks cannot be removed automatically. Therefore, the watchmakers clean each single engraving with a tooth pick.
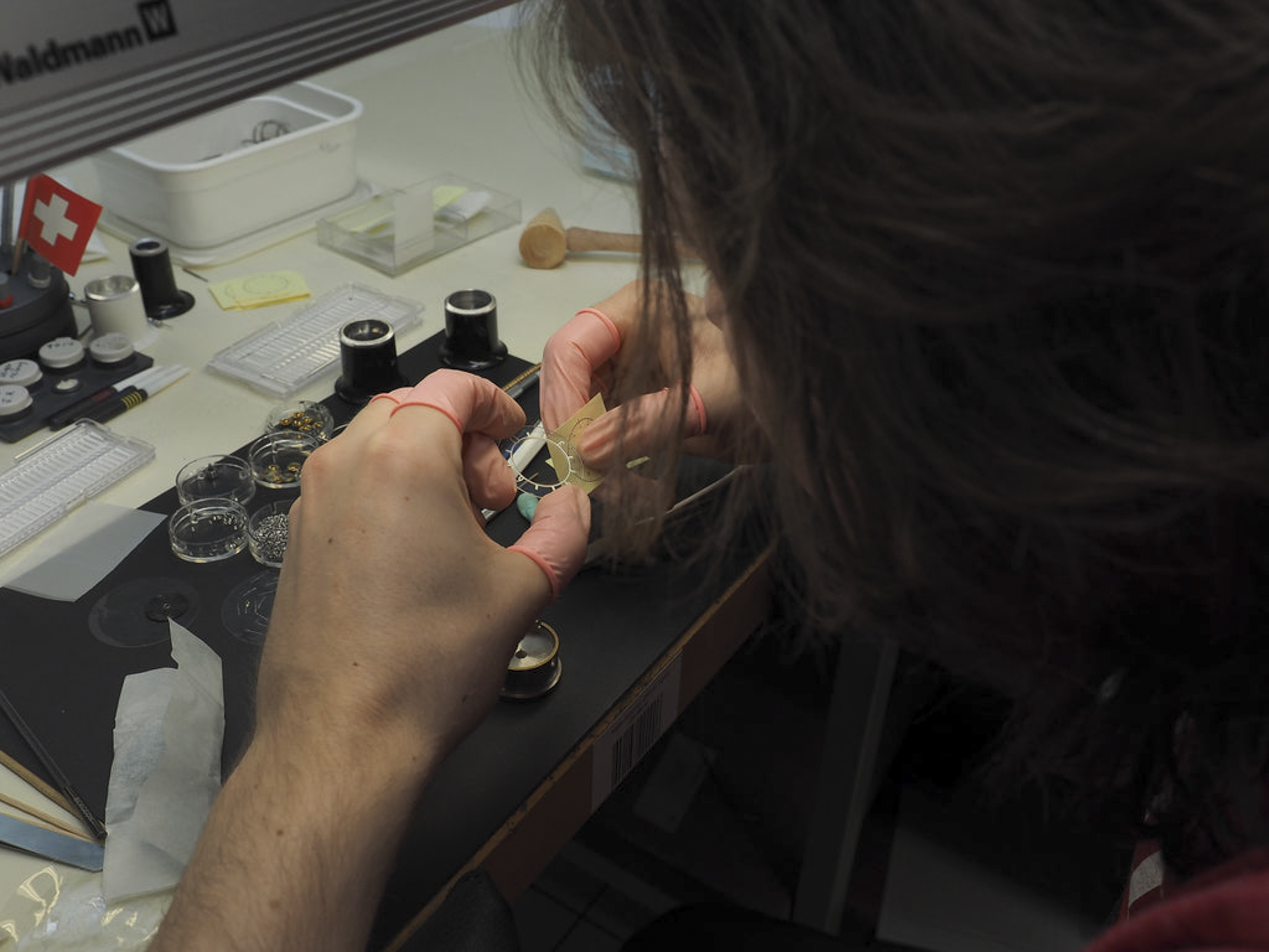
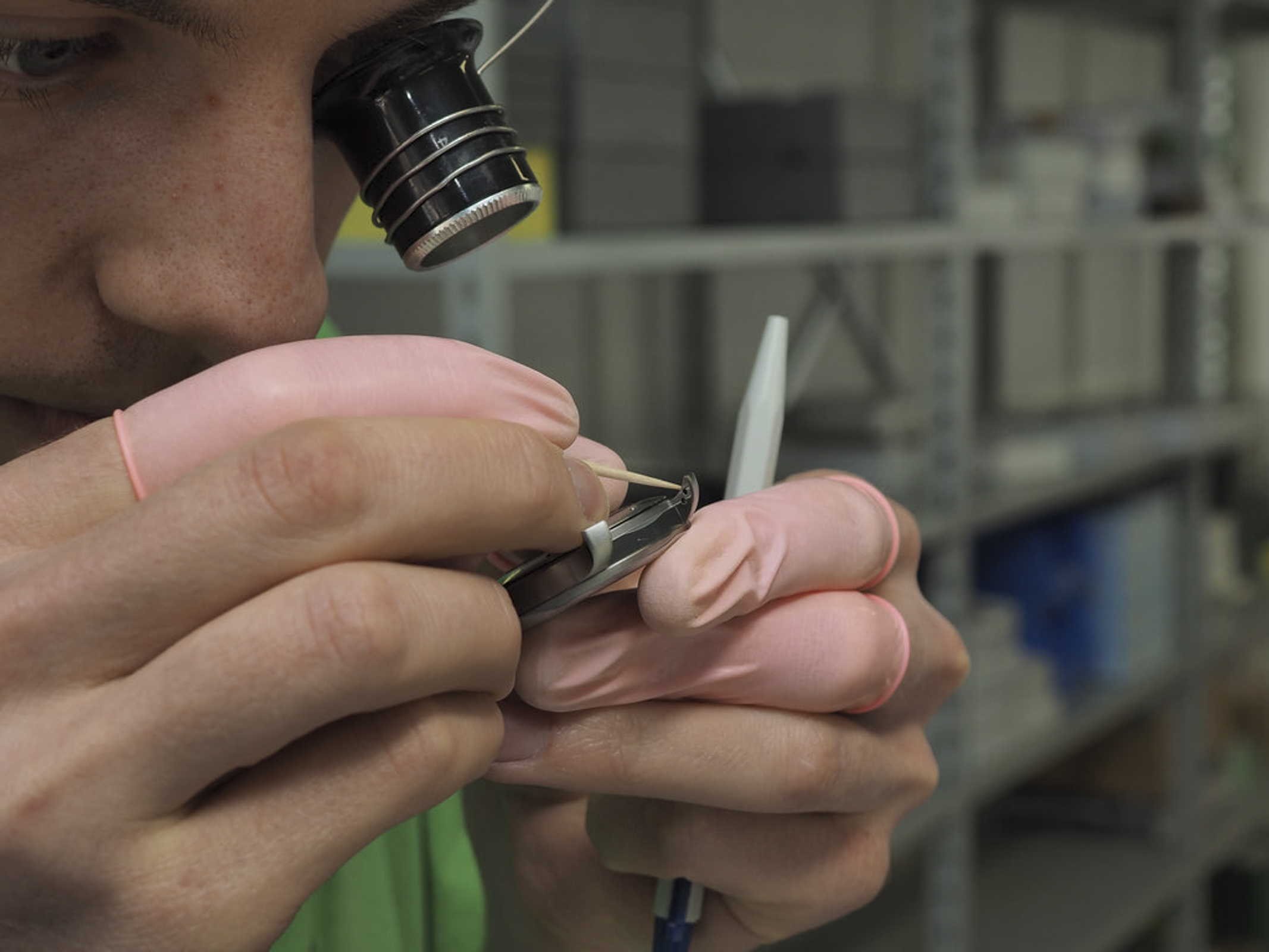
Assembling the dial: 3D dexterity is (not at all) all you need…
Now, with the components all QC-ed and cleaned, the 17.03 will finally assume shape. The process of putting the watch together starts with the assembly of the second timezone mechanism onto the Sellita SW-330 automatic movement. The next piece is a distance ring that ensures that the main dial element later levels with the GMT disk.
The watchmakers now build up the dial construction starting with the main dial plate. This plate harbours the circularly brushed outer ring beneath the sapphire donut as well as the 24h indicator ring. Two feet at the back secure the dial to the movement with the help of dedicated eccentric screws (the screw to the left of the crown stem).
The assembly is now ready to receive the GMT disk. What appears to be a quite plain and simple piece actually created and still creates a lot of headaches for us, our suppliers and the watchmakers themselves.
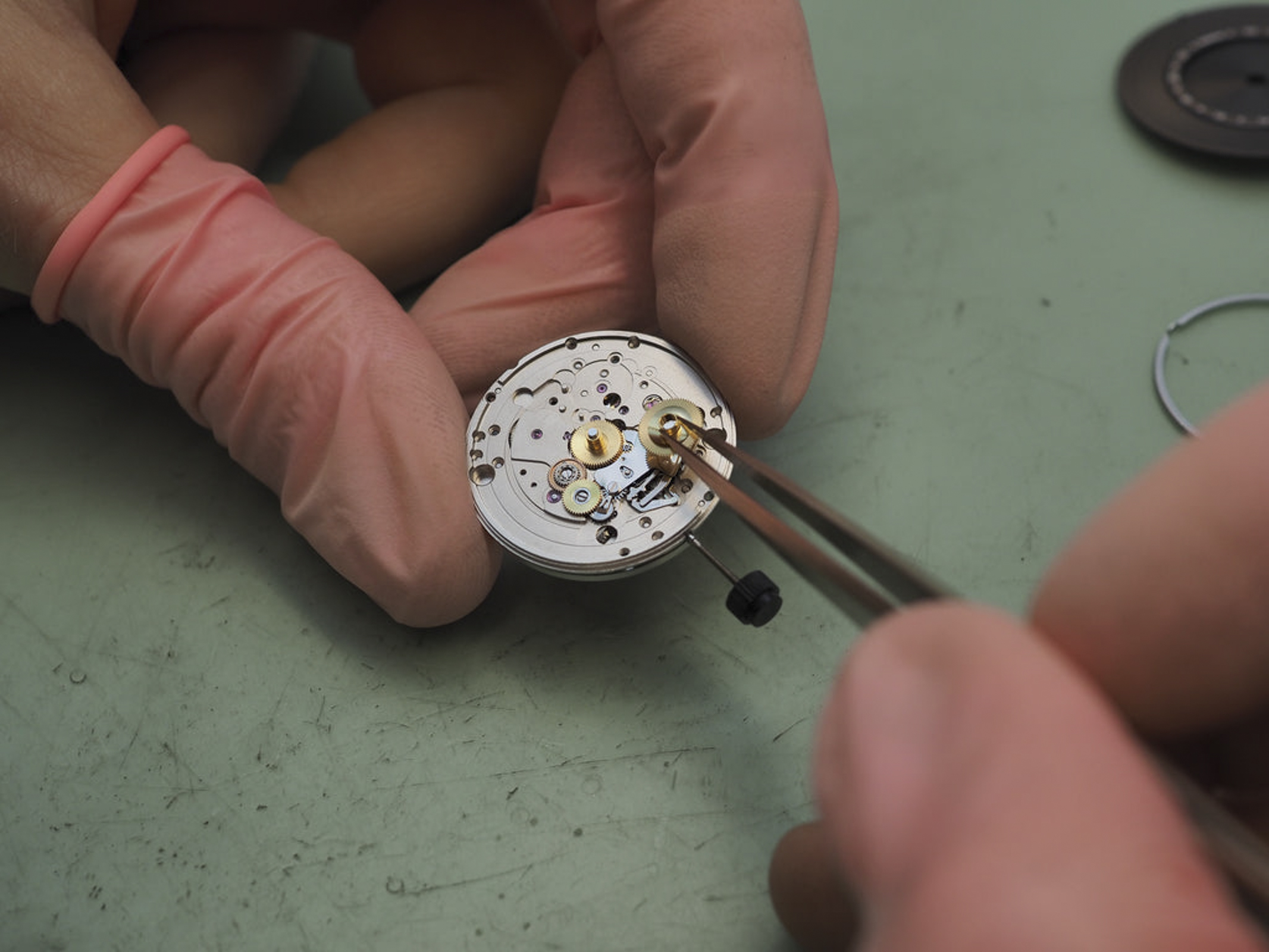
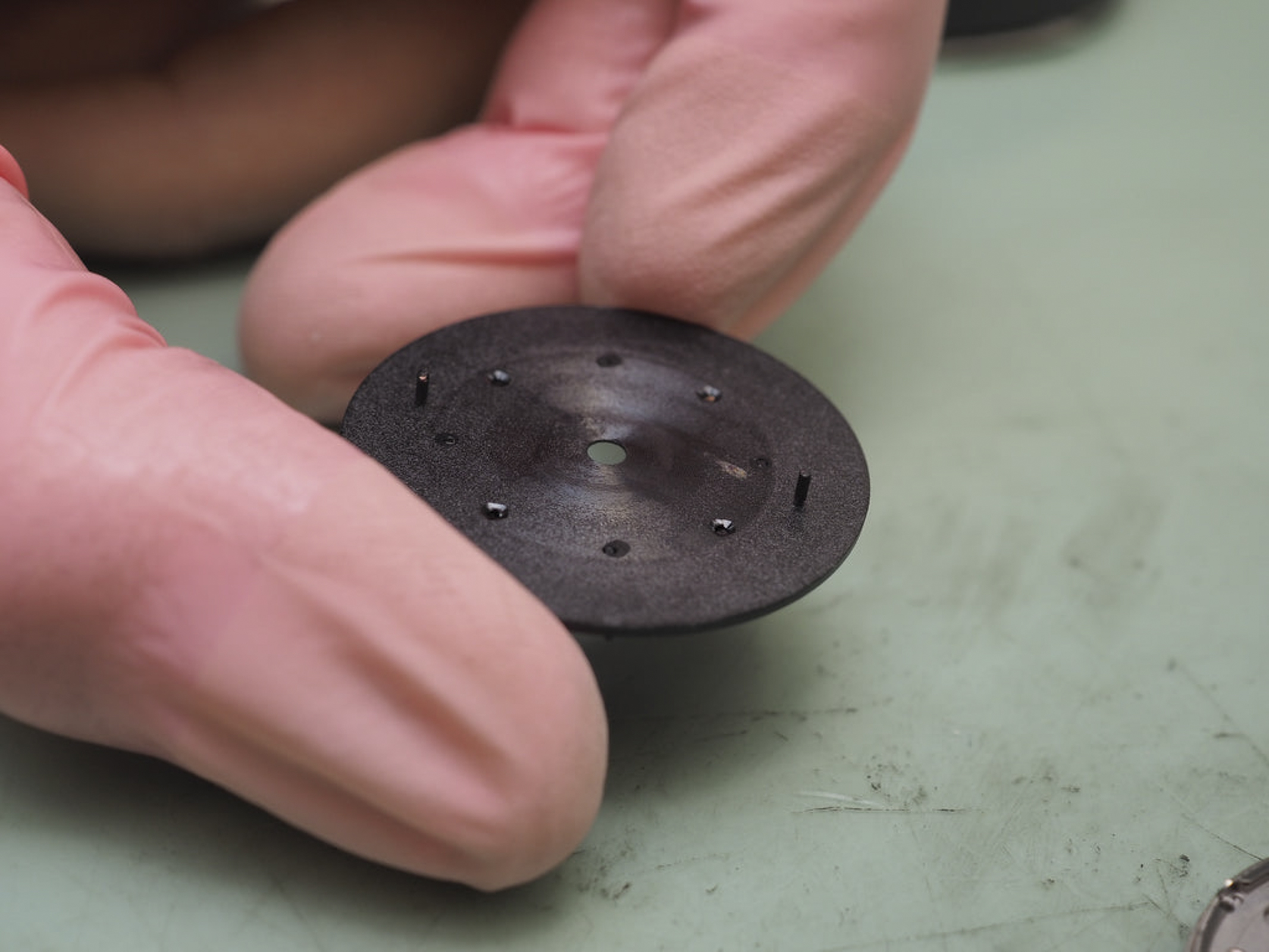
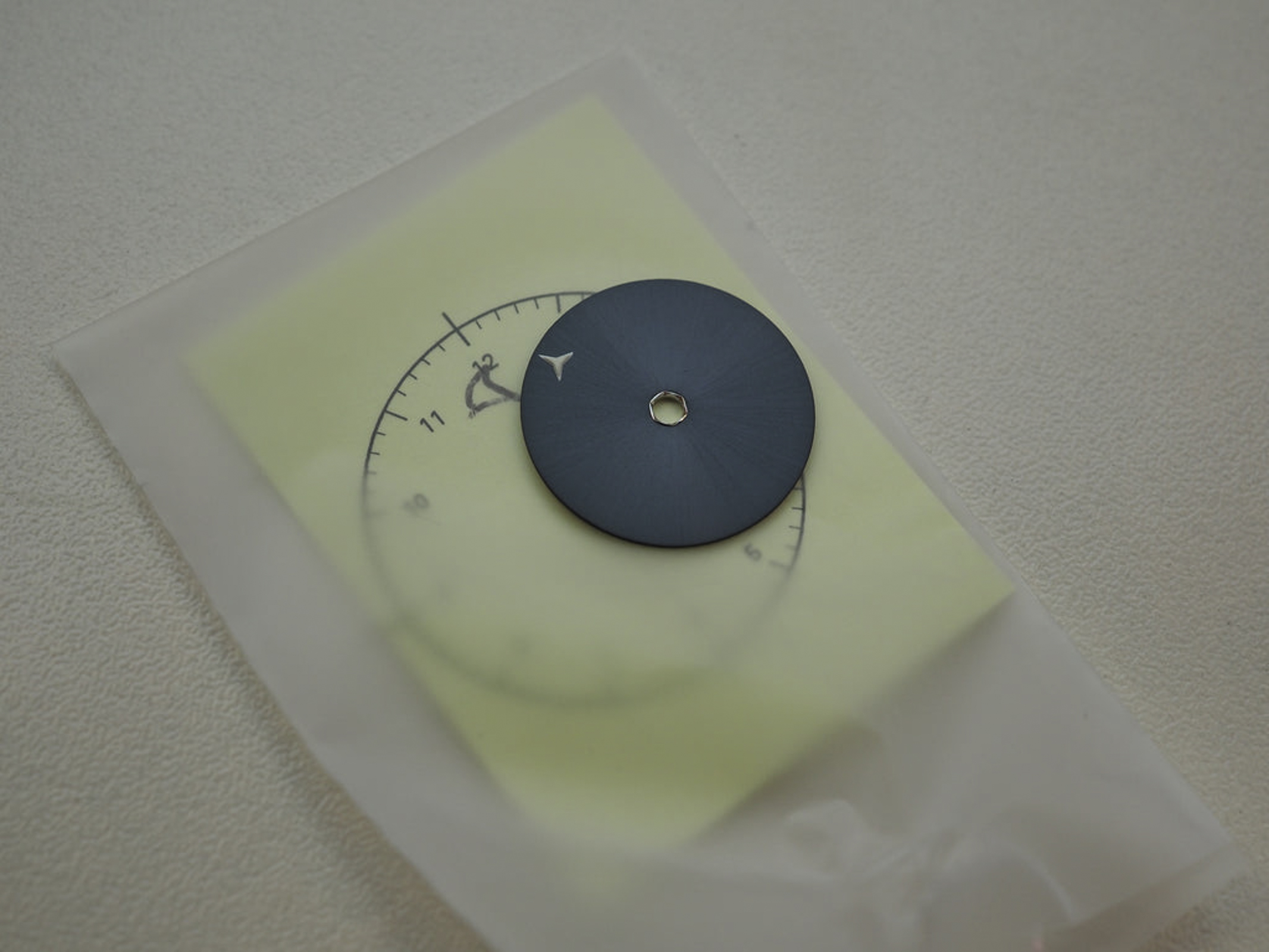
The challenges start already with the production of the disk: technically it is a hand, but in terms of its design and dimensions it is closer to a dial. The latter specification require that the disk itself is made at a dial factory, as firms specialising in watch hands are not equipped to handle ‘hands’ with such large and round shapes. Subsequently, the disk is shipped to our hands manufacturer who then mounts the tube which fixes the disk on the GMT wheel.
Due to the dimensions of the disk any impressions in production and assembly will be readily visible to the naked eye. Furthermore, the entire disk is always visible, which means that misalignments (such as eccentric or skewed insertion) will be more objectionable than in the case of a GMT hand or window (where such imperfections would be hidden).
This calls for special care and attention during production, quality checks and particularly while the disk is being fit to the watch. Each disk is carefully positioned with the pointing tool, and then checked for both planarity as well as centricity.


Only now can the sapphire donut be set in place. The donut needs to be slipped precisely into place, between the minute hand and dial, in a way that aligns it with the dial indications.
There are two notches on the donut ring at 12 and at 6 o’clock to precisely position it on the respective tappets on the dial.
The movement is technically now ready to be mounted in the case. Again, this is not really straight forward and will be covered in the next article...
- Dr. B